Unlock Breakthrough Heat Exchanger Designs with Gyroids
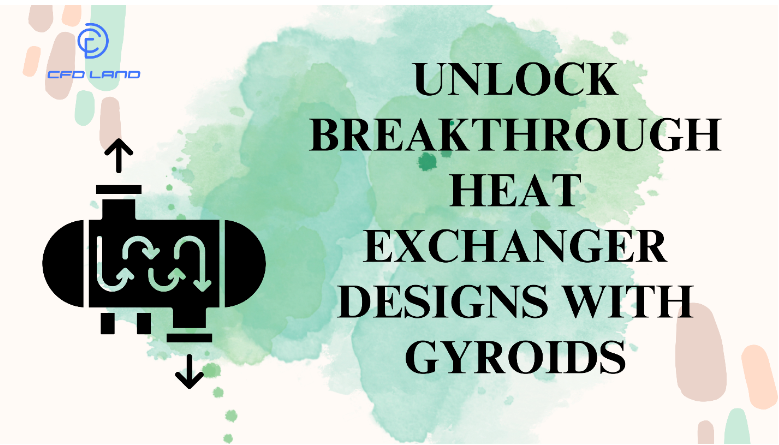
It may not seem like it at first glance, but heat exchangers play a very important role in the aerospace industry. In the following sections, we will describe one of the most important applications of heat exchangers. All heat exchangers, regardless of their complexity or application, can be studied using CFD heat transfer simulation. We have completed many projects in this field using ANSYS Fluent software at cfdland.com. Visit our site to see the capabilities of CFD.
Heat Exchangers in the Aerospace Industry
In airplanes during flight, the low air temperature at high altitudes causes a sharp drop in the temperature of the airplane fuel. This decrease in temperature is detrimental to the fuel combustion process; in fact, the temperature may drop so low that the fuel changes phase. Engineers have turned this challenge into an opportunity by using low-temperature fuel for thermal management of aircraft engines and other parts. This method increases the temperature of the fuel, eliminating the need for an additional thermal management system for the aircraft engine.
In some rockets, fuel with a very low temperature, and even in liquid phase, is used for the thermal management of the rocket engine.
Whether in an aircraft or a rocket, the fuel can receive heat from combustion inside the engine through a coolant fluid or be in direct contact with the engine. The device that plays a critical role in this process is a heat exchanger. The smaller and lighter it is, the more favorable it is for aerospace applications.
Suitable Heat Exchanger for Aerospace Industry
A suitable heat exchanger in the aerospace industry, due to its lightness and small volume, needs two features: 1. Within the minimum volume, the structure of the exchanger should be such that maximum contact between the fluid and the solid wall is established. 2. The walls of the exchanger should have minimum thickness without compromising structure resistance.
In this context, the company nTopology has used triply periodic minimal surfaces for the heat exchanger structure. For example, gyroids are one of their products that have a very high ratio of cross-sectional area to weight.
Two different gyroid designs. Adopted from “Unlocking Advanced Heat Exchanger Design and Simulation with nTop Platform and ANSYS CFX” by Maiki Vlahinos and Ryan O’Hara
Heat Exchanger Simulation by ANSYS Fluent
Many details are important in simulating a heat exchanger. Near the surfaces of the heat exchanger, the velocity of the fluid slows down, creating an area known as the boundary layer. With surface engineering, many efforts have been made to optimize this important area in terms of heat transfer. The amount of heat transfer at any point on the surface can be determined using Fluent simulation, and different materials and surface designs can be tested to enhance heat transfer in this way. Another issue is fuel impurities that may settle in the heat exchanger and block the fluid path. In Fluent, by simulating multiphase flows, it is possible to identify where particles settle, and by changing the design, these particles can be prevented from accumulating.
Read Also: Everything you need to understand about the basics of react native security
Due to the complex structure of gyroids in heat exchangers, meshing is very tricky. Fortunately, ANSYS can handle this task well with its various tools and features; however, the user must have a high level of experience and skill.
Until now, ANSYS Fluent has been the first choice of engineers and designers for simulating heat exchangers, and the capabilities of this software have been proven in numerous projects.
Conclusion
There are different methods for designing, studying, and optimizing a heat exchanger. Engineers can use experimental tests, theoretical methods, or perform CFD heat transfer simulations. All three methods are important, and a good heat exchanger is designed with the help of all three approaches.
In the aerospace industry, due to its unique characteristics, specialized heat exchangers are also needed. The greater the contact surface of the heat exchanger walls with the fluid and the lower its weight, the better. The structure of gyroids has these advantageous features.
Regardless of the type of heat exchanger or its application, simulation experts at cfdland.com can handle the simulations. Take a look at their completed projects on their site, and if needed, you can order your projects from them.