The Role of Injectable Component Manufacturer in the Pharmaceutical Supply Chain
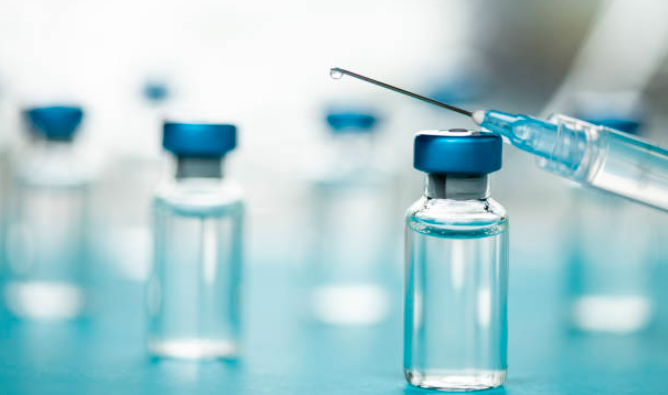
1. Introduction to Injectable Drug Delivery
Injectable drug delivery is one of the most effective methods for administering pharmaceutical formulations directly into the body. Injectable drug delivery provides rapid drug absorption, precise dosage, and high bioavailability, making it ideal for emergency care, biologics, and controlled drug release systems. Advances in biotechnology, materials science, and nanotechnology have led to the development of injectable formulations catering to various therapeutic needs.
Overview of Injectable Drug Delivery
An injectable components manufacturer refers to the administration of medications directly into the body using a needle and syringe or specialized delivery devices. This method bypasses first-pass metabolism and ensures the drug reaches its intended target quickly and efficiently. Common applications include:
- Emergency medications (e.g., epinephrine, insulin)
- Vaccines and biologics (e.g., immunotherapy)
2. Conventional Injectable Formulations
A. Solutions
- Simple liquid formulations, such as insulin and heparin, provide immediate therapeutic effects.
B. Long-acting and Controlled-Release Injections
- Depot injections: Slow-release formulations administered via intramuscular (IM) or subcutaneous (SC) routes (e.g., hormonal therapy, antipsychotics).
C. Biologic Injections
- Monoclonal antibodies: Used in immunotherapy for cancer and autoimmune diseases.
D. Device-Supported Injections
- Autoinjectors: Preloaded self-injection devices (e.g., EpiPen) that enhance patient compliance and safety.
3. Advantages of Injectable Drug Delivery
A. High Bioavailability
- Intravenous (IV) infusion provides 100% bioavailability, ensuring complete absorption into the systemic circulation.
Read also: Explore Everest Base Camp Helicopter Tour: An Adventure of a Lifetime
B. Rapid Onset of Action
- Ideal for emergency medications, anesthetics, and painkillers requiring immediate effects.
C. Precision Dosage
- Bypasses gastrointestinal metabolism, allowing for accurate and controlled drug administration.
D. Suitability for Biologics
- Peptide and protein-based drugs degrade in the gastrointestinal tract, making injectable administration essential.
E. Long-Acting Formulations
- Reduces dosing frequency, enhancing patient compliance and sustained drug release.
4. Challenges in Injectable Drug Delivery
A. Patient Compliance Issues
- Many patients fear needles, leading to preference for oral medications over injectables.
B. Need for Sterility
- Injectable formulations must be free from contamination, requiring strict sterile handling.
C. Pain and Discomfort
- IM and SC injections can be painful, leading to poor adherence.
D. High Production Costs
- Complex formulations (e.g., biologics, liposomes) require specialized manufacturing processes.
E. Risk of Side Effects
- Injections may cause local irritation, inflammation, or allergic reactions.
5. Future Trends in Injectable Drug Delivery
A. Smart Delivery Devices
- Wearable injectors that monitor and adjust drug administration in real time.
B. Needle-Free Injections
- Jet injectors and microneedles offer painless drug administration.
C. Injectable Nanomedicine
- Lipid nanoparticles and polymer-carriers improve targeted drug delivery.
D. Personalized Medicine
- AI and 3D printing enable customized pharmaceutical formulations tailored to individual patients.
E. Self-Administration Devices
- Growth in autoinjectors and digital health monitoring reduces hospital visits and enhances patient convenience.
6. Role of Injectable Component Manufacturers
The global pharmaceutical industry relies heavily on injectable component manufacturers who supply essential packaging and delivery equipment, such as syringes, needles, vials, cassettes, and closures. These components ensure the safe, sterile, and effective delivery of medications.
Key Functions of Injectable Component Manufacturers
- Maintaining Drug Stability and Sterility: Components such as glass vials, polymer containers, and elastomeric stoppers prevent contamination, oxidation, and moisture.
- Ensuring Accurate Dosage: Pre-filled syringes and autoinjectors improve dosing precision.
- Enhancing Patient Safety and Compliance: Innovations such as safety syringes and needle-free injectors minimize risks and enhance usability.
7. Challenges Faced by Injectable Component Manufacturers
A. Sterility and Contamination Control
- Injectable components must be manufactured in ISO 5 clean rooms to prevent microbial contamination.
B. Supply Chain Disruptions
- Events like the COVID-19 pandemic exposed vulnerabilities in supply chains, leading to shortages in vials, syringes, and stoppers.
C. Compatibility with Complex Biologics
- Monoclonal antibodies and gene therapies require specialized materials and packaging to maintain stability.
D. Sustainability and Environmental Concerns
- Manufacturers face increasing pressure to reduce waste, use recyclable materials, and minimize their carbon footprint.
8. Innovations in Injectable Component Manufacturing
A. Pre-Filled and Ready-to-Use Components
- Pre-filled syringes and ready-to-use (RTU) vials reduce contamination risks and improve manufacturing efficiency.
B. Smart Injection Devices
- Advances in smart injectors and wearable devices enable real-time monitoring and controlled dosing.
9. Conclusion
Injectable drug delivery continues to be a crucial pharmaceutical approach, offering high efficacy, precision, and adaptability. Despite challenges such as sterility, cost, and compliance issues, continuous research and innovation in injectable formulations and delivery devices are enhancing patient experiences and improving treatment outcomes. As technology advances, the future of injectable drug delivery promises safer, more efficient, and patient-friendly solutions.